The Manufacturing Process Behind Quality Paper Cups
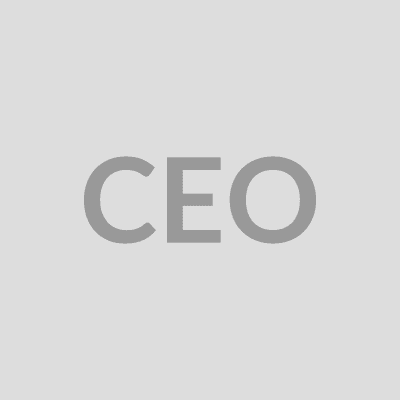
Production Team
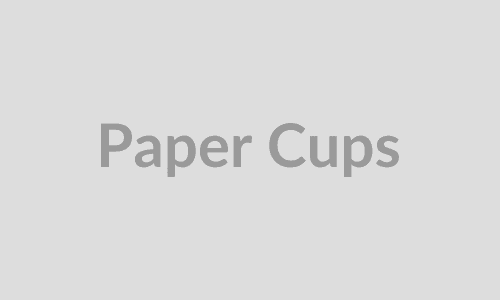
Paper cups are ubiquitous in our daily lives, from morning coffee runs to water dispensers in offices. Behind these seemingly simple products lies a sophisticated manufacturing process that ensures safety, quality, and functionality.
Raw Materials: The Foundation of Quality
The journey of a paper cup begins with careful material selection:
- Paperboard: The main component is food-grade paperboard, typically made from virgin wood pulp to ensure food safety. Premium cups use SBS (Solid Bleached Sulfate) board, known for its strength and smooth printing surface.
- Polyethylene Coating: A thin layer of food-safe polyethylene creates the crucial waterproof barrier inside the cup.
- Water-Based Inks: For printed designs, non-toxic water-based inks ensure safety for food contact.
The Manufacturing Process
1. Paperboard Preparation
The process begins with large rolls of paperboard that undergo quality inspection for consistency in thickness, weight, and brightness. The paperboard is then unwound and fed into the cup-making machines.
2. Printing
If the cups will feature branding or designs, printing happens before cup formation. Advanced flexographic or offset printing techniques apply designs to the paperboard's outer surface. The printed material then goes through drying stations to ensure the ink is completely set.
3. Cutting and Forming
The paperboard moves through precision cutting machines that:
- Cut the board into individual blanks (cup bodies)
- Create notches to facilitate proper folding
- Shape the top rim area and bottom base
The blank is then wrapped around a mandrel (a cone-shaped forming device), and heat is applied to create the cylindrical shape. This is a critical step that determines the cup's structural integrity.
4. Bottom Sealing
A separate circular piece of paperboard is cut for the bottom of the cup. This piece is heat-sealed to the cup body, creating a watertight bottom seam. The quality of this seal is essential for preventing leaks.
5. Rim Formation
The top of the cup undergoes a special process called "rimming" or "curling," where the edge is rolled outward to create a comfortable drinking surface and add structural strength. This rim also provides a secure fit for lids.
6. Quality Control
Throughout the manufacturing process, rigorous quality control measures ensure:
- Structural integrity testing for leaks
- Dimensional accuracy checks
- Visual inspections for printing defects
- Microbiological testing for food safety
Advanced manufacturers employ vision systems and automated leak testing to maintain consistent quality across millions of cups.
Innovations in Paper Cup Manufacturing
The industry continues to evolve with innovations like:
- Bio-based PE Coatings: Derived from plant sources rather than petroleum
- Aqueous Barrier Coatings: Biodegradable alternatives to traditional PE
- Double-wall Technology: Enhanced insulation without the need for sleeves
- Embossing Techniques: Improved grip and heat insulation
Kiran Paper Products' Approach
At Kiran Paper Products, our paper cup manufacturing integrates traditional craftsmanship with modern technology. Our facility employs high-speed forming machines capable of producing up to 120 cups per minute while maintaining rigorous quality standards.
We've invested in sustainable innovations, including reduced-weight paperboard that maintains strength while using less material, and are exploring compostable barrier options to enhance end-of-life disposal.
The next time you hold a paper cup, you can appreciate the sophisticated engineering and quality control that allows this seemingly simple product to safely deliver your favorite beverage.
Subscribe to Our Newsletter
Stay updated with our latest articles, product updates, and industry insights.